Lubrication systems
Automatic Lubrication Systems
Accurate, versatile, simple and reliable.
BRAUN CORPORATION offers a wide range of equipment and components, as well as design and implementation in automatic lubrication systems. Our product range includes lubricators, resistance accessories, injectors, manifolds and accessories for use in a variety of systems. Each of our automatic lubrication systems can be used in a variety of industry sectors, from specific applications to broad machinery lubrication, each of which helps extend machinery life and maintain production efficiency.
Advantages of an Automatic Lubrication System
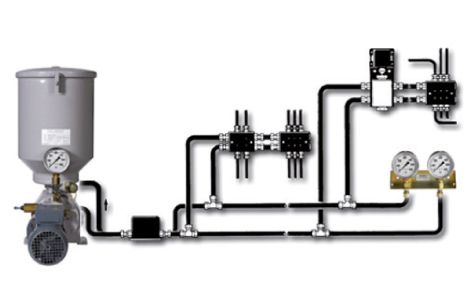
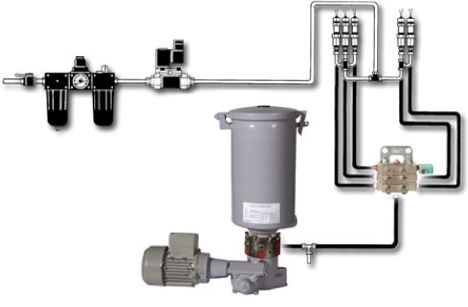
Proven technology with reliable supply of lubricant to all points while equipment is in operation.
Better equipment performance per day and less maintenance time.
Maximize equipment life and help avoid unplanned equipment downtime, costly repairs, and unscheduled downtime.
Acensial for critical equipment with advanced monitoring systems that warn of problems before failures occur.
Create a safer work environment for maintenance personnel.
Eliminate the mistakes of the human factor.
Systems built to withstand harsh environments.
Environmentally friendly by reducing oil consumption and fat waste.
Suitable for many applications
Applications
- Mining
- Metal forming
- Wind power
- Farming
- Automotive
- Cement
- Food industry
- Gear spray
- Machine tool
- Petroleum gas
- Railway
- Steel
- And many more
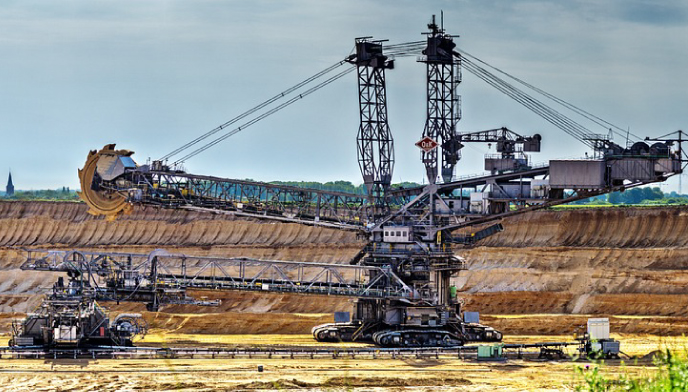
Applications
- Mining
- Metal forming
- Wind power
- Farming
- Automotive
- Cement
- Food industry
- Gear spray
- Machine tool
- Petroleum gas
- Railway
- Steel
- And many more
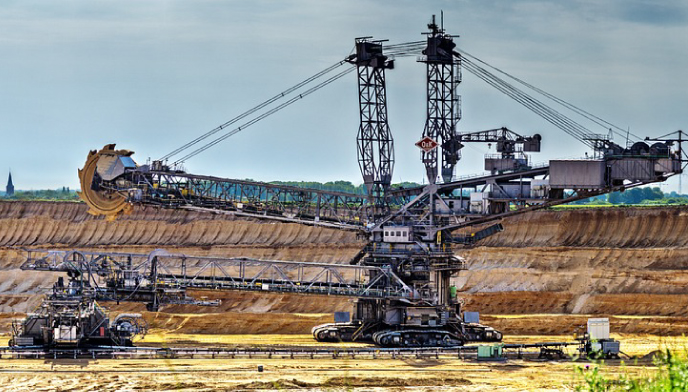
Custom Equipment
Dual Line lubrication systems are found in virtually every industry where continuous operation is required. From steel to paper production, from mining equipment to food industry machines, the automatic application of the lubricant provides significant benefits for the user of the equipment. There are several components that are used in the design of a Dualine lubrication system, including valves, lubricators, reversing valves, central stations, controllers, and spray systems.
Valves
Metering valves are the heart of Dualine lubrication systems. They are mounted close to the lubrication points and are hydraulically operated by pressure from the first and then the second of the two supply lines. In each pressurization cycle, they indirectly discharge fixed volumes of lubricant to the bearing or lubrication point.
Central Stations
Central stations include lubricator, cycle switch, and reversing valve. Some are mounted on a plate to facilitate installation.
Reseve Valves
These valves change the flow and direction of pressure, causing the divider valves in the system to activate.
Spraying Systems
Used to lubricate large gears and pinion assemblies.
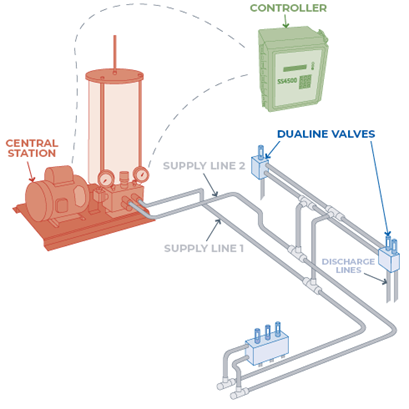
Advantage
Economical system for more than 20 lubrication points.
Lube points can be easily added without redesigning the entire system.
A blockage between the feed line and the bearing will not block the system; The remaining bearings will continue to work..
Positive lubrication indicators for each point of support.
Ability to positively displace a wide range of lubricants from light oil to grade 2 grease.
The lubrication discharge volume in each bearing is fully adjustable even after start-up.
Progressive Lubrication Systems
Progressive lubrication systems are generally used in a wide variety of industrial machinery and equipment. The pumps are connected to divider valves, some of which are modular, allowing for easy installation, modification, and maintenance.
The M2500G, 3000 and PVBM series progressive divider valve manifolds distribute and provide incoming oil or grease to the bearing points. A typical divider valve manifold consists of an inlet section, three to ten valves, and an end section. One set can serve up to a maximum of 20 lubrication points. The individual divider valve blocks have a built-in discharge piston and outlet check valves. Blocks are offered in various outlet sizes. The discharge capacity of a block is determined by varying the diameter of the piston in the valve block.
The M2500G, 3000 and PVBM series progressive divider valve manifolds distribute and provide incoming oil or grease to the bearing points. A typical divider valve manifold consists of an inlet section, three to ten valves, and an end section. One set can serve up to a maximum of 20 lubrication points. The individual divider valve blocks have a built-in discharge piston and outlet check valves. Blocks are offered in various outlet sizes. The discharge capacity of a block is determined by varying the diameter of the piston in the valve block.
Progressive Divider Valve Sequence of Operation
The individual valve blocks operate in a “progressive” sequence. During operation, the piston within the block must complete a discharge cycle before another piston begins to work. As long as lubricant is delivered under pressure to the inlet section of the divider, the manifold valve blocks will continue to function progressively.
When the flow of lubricant to the inlet block is blocked, the movement of the piston stops. When flow resumes, piston movement begins at the same point in the discharge cycle. The supply lines supply lubricant from the valve block to the individual lubrication points. If a discharge line becomes blocked, it will stop the operation of all valves. Indicators are available to alert you to a crash.
When the flow of lubricant to the inlet block is blocked, the movement of the piston stops. When flow resumes, piston movement begins at the same point in the discharge cycle. The supply lines supply lubricant from the valve block to the individual lubrication points. If a discharge line becomes blocked, it will stop the operation of all valves. Indicators are available to alert you to a crash.
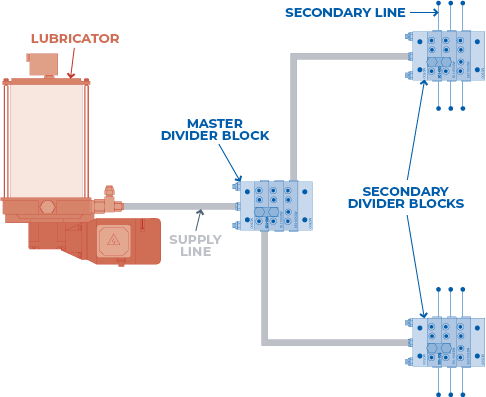
Single Line Systems
Single line lubrication systems are less complicated, simple installation. Facilitates the supply of small doses of oil through Dosing Units. Electric and manual pumps are available to guarantee a discharge of up to 200 cc / minute. The oil dosage is proportional to the pump pressure and the oil viscosity. They are low pressure oil lubrication systems for light, medium and heavy machinery that require up to 100 lubrication points.
Automatic systems are ideal for machinery that requires an uninterrupted discharge of oil, either on a regular or continuous basis. Automatic systems are actuated by a self-contained timing mechanism or by a mechanical actuation mechanism connected to the equipment being lubricated.
Advantage Compact, inexpensive and relatively easy to operate and maintain. The system is ideal for machinery or equipment with a large number of lubrication points. A precisely controlled oil discharge is supplied to each point while the machine is running. The system provides a clean film of oil between critical bearing surfaces to keep friction and wear to a minimum. Machinery life is prolonged and production efficiency is maintained.
Automatic systems are ideal for machinery that requires an uninterrupted discharge of oil, either on a regular or continuous basis. Automatic systems are actuated by a self-contained timing mechanism or by a mechanical actuation mechanism connected to the equipment being lubricated.
Advantage Compact, inexpensive and relatively easy to operate and maintain. The system is ideal for machinery or equipment with a large number of lubrication points. A precisely controlled oil discharge is supplied to each point while the machine is running. The system provides a clean film of oil between critical bearing surfaces to keep friction and wear to a minimum. Machinery life is prolonged and production efficiency is maintained.
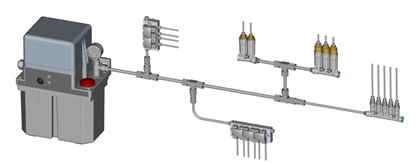
Contact Us
- Phone: +1 (954) 989-3530
- Fax : +1 (954) 989-3532
- sales@brauncorpusa.com